Prefab sprouts: entire home to be dropped onto London Fields building
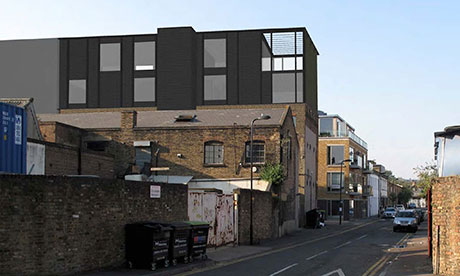
Sketches of how the prefab might look once installed
An entire home is to be lowered onto the roof of a brick warehouse in London Fields this month.
The project has been undertaken by Old Street-based architects Simon Conder Associates (SCA), and will involve dropping a 350 square metre prefabricated structure onto the roof of a 1920s warehouse on Fortescue Avenue by crane.
The two-storey structure, built for designers Caz Hildebrand and Lisa Vandy, who own and work out of the warehouse beneath, will be lowered onto a steel-and-timber ‘platform’ which has been designed to spread the load of the new build onto the external walls of the warehouse.
Simon Conder, founder of SCA, oversaw the project and admits the project was “a bit of a tough ask” because of its sheer scale. “It’s quite large relative to the building below it, which because of its age doesn’t have proper foundations as we understand them today. So structurally it’s a novel build to be able to put so much weight onto such a limited
structure below.”
Working in a built-up area has also been a challenge, Conder explains.
“If we did this conventionally, the build would go on for months and cause disruption, and road closures.
“With the prefab, we put it together in a factory in Barnsley and the main building goes up in just three weeks –it’s about minimising inconvenience.
“Also, we’re providing a shell for people to work in – in the dry – after just three weeks, whereas that could be many months using regular construction methods.”
As well as giving design-conscious homeowners a new way to settle down in the city, prefabricated homes are creating new opportunities for social housing.
Just last month, a partnership between the YMCA and architects Rogers Stirk Harbour – the people behind the ‘Cheesegrater’ – led to the installation of 36 prefabricated “Y:Cube” homes in Mitcham, for formerly homeless local residents, let at two-thirds of market rents. Deputy Mayor for Housing Richard Blakeway described it as “a fantastic example of the innovative projects we support to address a range of housing demands”.
Prefab housing has a long legacy in the UK, having been introduced to the nation in 1944 by Churchill’s Temporary Prefabricated Housing Programme, as the country faced up to a major housing crisis in the wake of the Second World War. Factories which had been producing aeroplanes were refitted to build sections of the new homes, and over 150,000 were produced by 1951.
Conder suggests that a new wave of prefab projects is being spurred on by newly-available materials including cross-laminated timber, or CLT, which has significant benefits over concrete construction in terms of both build time and environmental impact. Conder says: “When we investigated prefabs a decade ago we needed around 60 units to make it viable. Now we’re using it on individual houses, and CLT has made a big difference.’
While the London Fields project is hardly social housing, Conder equally doesn’t consider it ‘high-end’ construction.
“It’s a pretty basic building in many ways,” he says. “Our clients wanted a simple living space – like the lofts we used to have in Hackney before the bankers moved in!
“In the old days, luxury was gold taps, but now the luxury is just space.”